Printed photovoltaics: challenges and issues
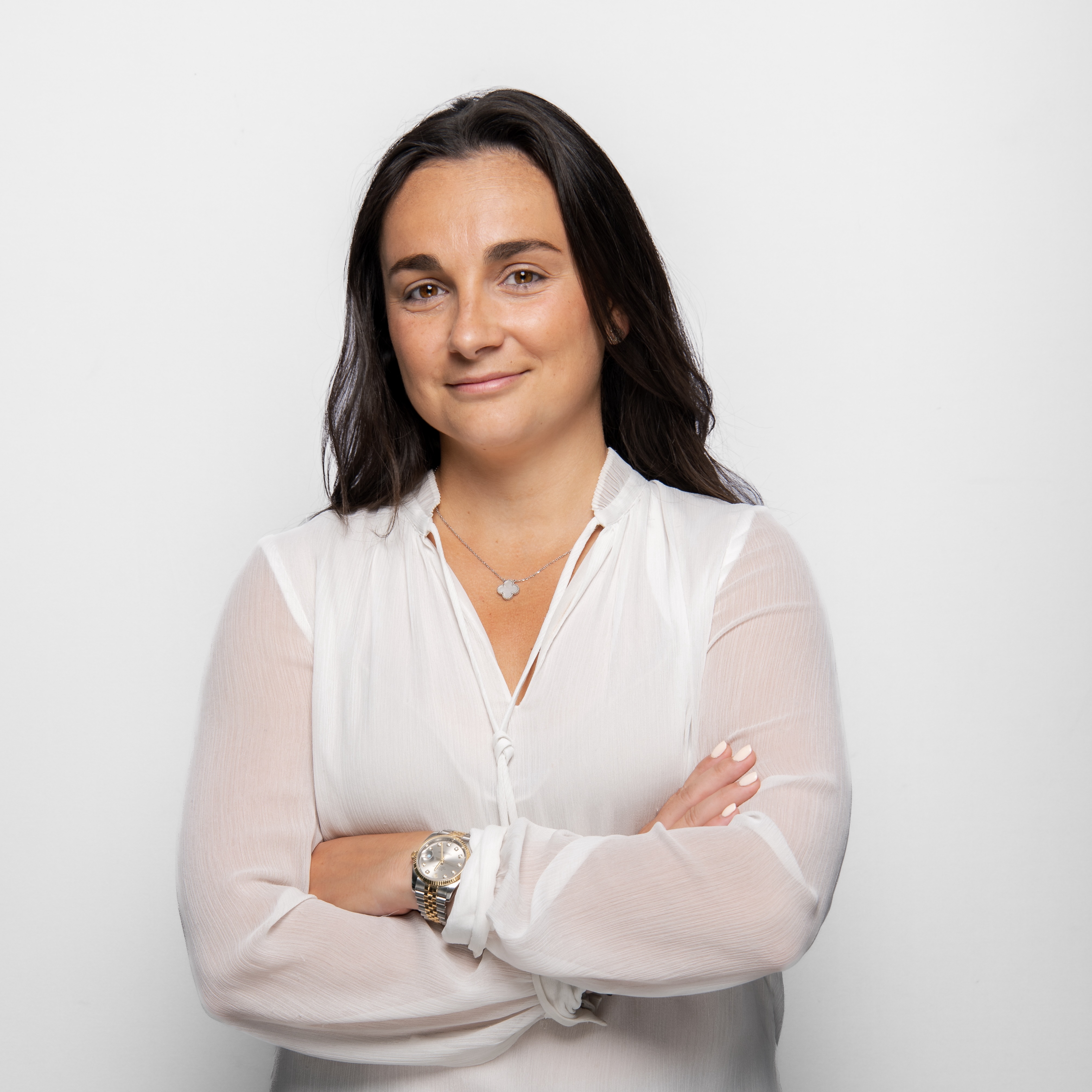
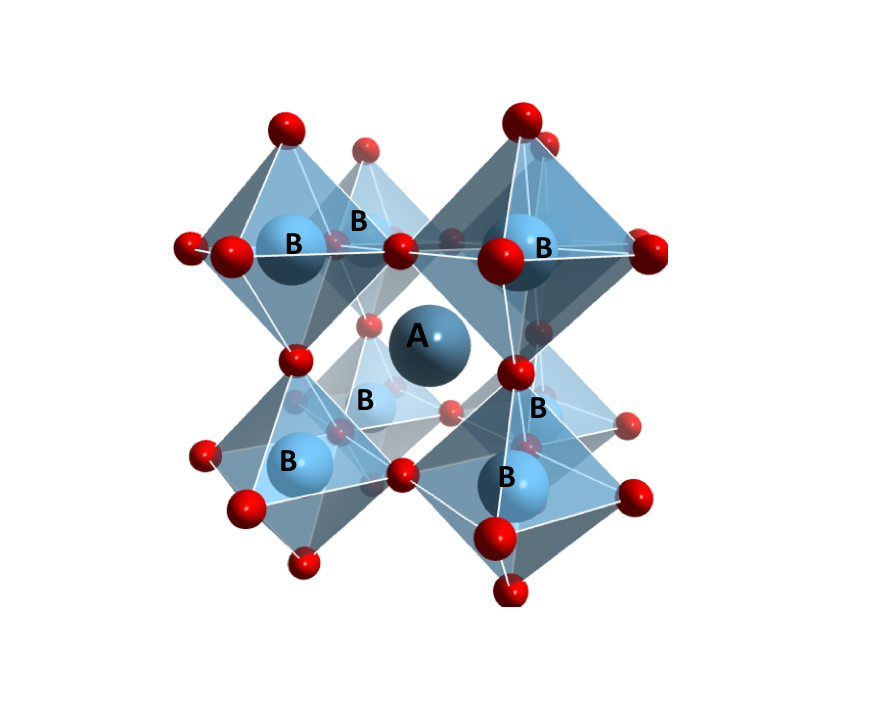
This technology, still under development, combines cost, flexibility and environmental benefits, with laboratory yields almost equivalent to existing ones. But what makes these cells so special, and what challenges still need to be overcome before they can be adopted on a large scale?
- The challenges of manufacturing a solar cell
Current solutions for making photovoltaic cells involve stacking different layers of materials that make up the electrodes, charge carriers and semiconductor that reacts with light, as well as other additional layers to stabilize the whole.
Each of these layers must be chemically and physically compatible with neighboring layers. The surface electrode must be transparent, which in scientific terms is referred to as transmittance - the ability of a material to allow light to pass through. Ideally, this should be 100%, but in practice, the surface electrodes of today's solar cells have a transmittance of around 85%. Only graphene, as a conductive material, has a transmittance of over 90%. Can you see the headache? Now let's add a cost constraint so that the technology can really leave the laboratory, namely an average cost per m² of less than €100, or around 30 centimes per watt produced.
GRAPHENATON Technologies SA (GTSA), via its GRAPHENATON Labs laboratory, is focusing on these aspects in its research programs to develop a solar cell that is sufficiently efficient, yet environmentally responsible and economically viable.
The challenges addressed concern all layers, and more specifically the electrodes and semiconductor material. For the former, GTSA is working on the use of graphene in particular; for the latter, GTSA has launched a research program on perovskites.
The R&D teams were also faced with two constraints: firstly, they had to work in an ambient environment in order to guarantee tomorrow's industrial possibilities at reasonable prices; secondly, they had to print the entire cell in a single process in order to be able to envisage large volumes simply, and thus define the most suitable inks and substrates.
- Tin perovskites: a promising alternative to lead perovskites
Perovskites, particularly lead-based ones, have attracted the attention of researchers due to their remarkable efficiency and laboratory performance close to that of silicon (27.6% efficiency for silicon vs. 26.1% for perovskites) [1]. However, lead toxicity poses long-term health and environmental problems. GTSA offers a less toxic alternative, tin perovskites.
Tin perovskite solar cells use a known metal halide perovskite structure, but where tin, which is far less toxic, replaces the lead traditionally used [2]. This active layer has favorable properties for converting light into electricity, with less environmental impact. It can also be made from an "ink", and can be custom-tailored to suit different materials [3][4][5]. The first prototypes have been produced, demonstrating their technical feasibility with low-cost materials.
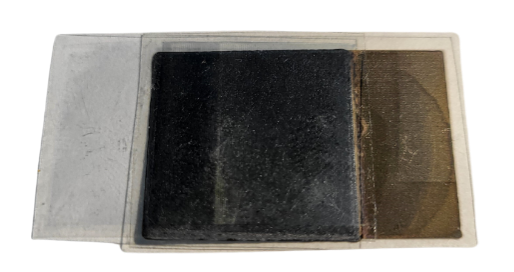

Figure 1: GTSA prototype solar cell printed in tin perovskite 2 cm x 2 cm (left).
Current response of cell protype in light and dark (right)
- Innovative printing techniques...
What really sets GTSA's perovskite-based solar cells apart is the way they are manufactured. Unlike traditional solar cells, these cells can be printed onto flexible polymeric substrates.
Functional inks" are thus developed, containing all the precursors, or building blocks, that go on to form the perovskite. Once deposited by printing, the various components self-aggregate to form a thin crystalline structure capable of reacting with light.
Printing techniques such as inkjet enable these thin layers to be deposited precisely and efficiently. They are also less costly than conventional methods: only as much ink as is needed is consumed, and annealing processes are carried out at much lower temperatures than conventional methods, i.e. 120°C or less, compared with over 1,000°C for silicon purification. This avoids costly waste treatment processes, minimizes excess energy consumption during manufacture, and eliminates the need for a highly constrained cleanroom production environment.
These printing technologies could also be used to produce films that go beyond the usual panel dimensions (1.65 m²/60 cells, 2 m²/70 cells) for new uses.
4 ... Challenges ready to be met
However, there are still many challenges to overcome.
First of all, the active layer itself. Perovskites, particularly tin perovskites, are more sensitive to moisture and oxygen, both during the manufacturing process and over the long term, which can lead to rapid performance degradation. Research efforts are underway to develop new functional inks with perfect inter-compatibility and high stability for printing in a standard environment, aspects which GTSA is actively investigating.
Furthermore, to be fully functional and capture a maximum amount of light, the layers between the photosensitive part and the surface must be not only conductive but also transparent. The materials of choice for transparent surface electrodes are currently ITO (indium-doped tin oxide) layers, which use rare earths. In addition to the lack of flexibility of these layers, the use of these rare earths poses problems of sovereignty (90% of reserves are held by China, Vietnam, Brazil and Russia, and more specifically for indium, China alone produces 2/3 of global consumption [6][7]). This is why GTSA wants to turn to graphene electrodes. Made of carbon atoms arranged in a hexagonal mesh, this material, whose transparency and conductivity equal or surpass ITO, is a perfect candidate. In this application, we use a polymer film on which a thin sheet of graphene has been vacuum-grown in a controlled manner, and then used as a printing substrate. However, the main challenge lies in its economic viability, as it currently costs around €5,000/m². For this reason, GTSA is also investigating the use of polymers incorporating carbon nanotubes or metal nanowires for surface electrodes. But graphene can also be used as an ink. In this case, it is opaque, but can still be used as a background electrode (the electrode at the back of the cell), taking advantage of certain properties such as its excellent conductivity.
- Outlook
Ambient-printed solar cells based on tin perovskite represent a major breakthrough in the field of photovoltaic cells, making them lead-free. Their potential to offer a less toxic, flexible and cost-effective alternative is well established.
GTSA's R&D subsidiary GRAPHENATON Labs, based at the Université Paris Cité, has embarked on research programs which, while validating scientific hypotheses, have yet to deliver energy performance to rival existing solutions. A number of laboratories around the world are working on similar issues, and results are progressing rapidly.
GTSA considers that it should be able to supply printed photovoltaic cells on a pre-industrial basis in 2025, particularly in view of economic constraints.
The commercial applications of these photovoltaic cell films are immense, and could represent a revolution in large-scale photovoltaic power generation.